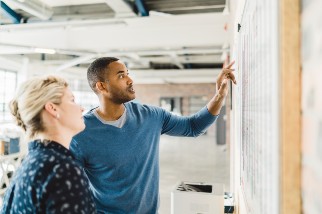
As companies face increased operational complexity, safety leaders have been turning to high reliability principles to reduce errors, lower the risk of failure and improve safety.
High reliability theory was developed in the 1980s as an opposing viewpoint to normal accident theory, which contends that failure is inevitable within highly complex systems such as air traffic, space programs and nuclear power plants. The five principles of high reliability organizations (HROs) are:
- Deference to expertise
- Preoccupation with failure
- Reluctance to simplify
- Sensitivity to operations
- Commitment to resilience
“When those high reliability principles are implemented and executed effectively, each of them interlocks with the different components of the safety management system,” says Cory Worden, Ph.D. (ABD), CSP, CSHM, CHSP, past administrator of our Healthcare Practice Specialty. “If you’re setting up safety committees, then you’re deferring to experts. If you’re doing a hazard analysis and risk assessment, then you’re getting into preoccupation with failure. If you’re putting in the most effective hazard controls, you have to be looking at the reluctance to simplify.”
ASSP’s Healthcare Practice Specialty and Blacks in Safety Excellence (BISE)/Hispanic Safety Professionals common interest group communities discussed ways to achieve high reliability by engaging a diverse representation of workers in safety and operational processes.
Principle 1: Deference to Expertise
People in HROs value insights from those with the greatest expertise in an area — even over those with the highest seniority, according to a report from the Agency for Healthcare Research and Quality (AHRQ). To achieve this, organizations must have processes that identify and enable those with the most knowledge and experience to share their perspectives.
“We need to give those people with expertise room so they can make the decision,” says Mery Sennett, M.S., M.A., of ASSP’s Hispanic Safety Professionals Common Interest Group. “We need to listen to people with fresh voices because they are seeing things that management doesn’t see. When someone with no power can speak up and give their opinion — that’s awesome.”
To fully achieve this, organizations must establish open pathways for all workers to share their opinions through cross-functional meetings, project groups and safety committees. They should also create cultures where workers feel comfortable speaking up because leaders value consistent learning from internal specialists and recognize their expertise as an asset, Sennett says.
Principle 2: Preoccupation With Failure
A preoccupation with failure means developing awareness of the possibility of failure and being alert to small signs of potential problems — but not to the point of “toxic paranoia,” Worden cautions.
“We want to be able to identify, assess and control hazards and threats the best we can, but not at a level that’s going to adversely affect operations,” he says.
HRO workers deliver the right training to the right people and ensure operational processes are all working effectively and efficiently, says BISE’s Stephanie Johnson, CSP, CHMM.
They also improve their processes by encouraging employees to report near misses and viewing those reports as opportunities to dissect the systems in place and proactively address any potential issues.
Reporting near misses “shouldn’t wait until escalation to a high level of severity,” Sennett says. “Companies need to engage everyone and let them know how they do this and follow up. It’s on everyone, everywhere, every day.”
Principle 3: Reluctance to Simplify
Leaders of HROs understand that work is complex and dynamic, and they refuse to simplify their understanding of how or why things succeed or fail in their work environment, according to AHRQ.
In safety, Worden says it’s possible to oversimplify — “I told them where the hazard was and told them to be careful” — yet don’t actually address the risk.
Sennett recommends using improvement tools like root-cause analyses to avoid simple answers for failures or near misses — such as human error or lack of training. An incident investigation shouldn’t just explain what happened. It should identify how to fix the problems the incident revealed.
“Remember, the purpose of the investigation is to mitigate the risk for tomorrow,” Sennett says.
Oversimplification also happens when there’s a lack of diverse voices.
“It is important you have the right people there and bring together those who have a responsibility for or expertise in a system and have a conversation about what is the best way to solve this,” Johnson says.
Principle 4: Sensitivity to Operations
Safety professionals in HROs look at their work in the context of the entire organization’s goals and operations.
“We want to increase safe work conditions and safe work practices in a way that will enhance operations and put controls in place that will make it safe while still achieving the objectives,” Worden says.
He compares it to conducting COVID-19 tests: It would be safest for employees to not conduct the tests, but that achieves nothing. So, the safety professional’s goal is to design the safest way to conduct the test.
Organizational and safety leaders must look at “the impact of our decisions on the people at an operational level” Johnson says — particularly the impact of a change or of not making a necessary change.
Sennett also says safety leaders should consider the risk of complacency on operations. She cited an example of a worker who performed the same job each day for more than a decade, then had an incident that led to the amputation of three fingers. The worker didn’t lack any amount of safety training, but his routine had become rote and his attention waned.
HROs can combat this by conducting daily safety meetings, implementing policies to recognize errors and make improvements, and offering continuous feedback.
Principle 5: Commitment to Resilience
Because leaders in HROs accept the risk of failure, they implement proactive preventive measures to reduce that risk and practice responding to challenging situations, AHRQ writes. Commitment to resilience can reduce both the frequency and severity of adverse events.
For Johnson, this starts with the proper attitude toward errors.
“If the attitude is ‘It should not have happened and we’re attacking people when it happens,’ we’re not getting at a root cause and we get underreporting,” Johnson says. “We don’t want to go to the blame game. We really want to go to the root cause and resolution so we can prevent that from happening in the future and we’re in a better position to respond.”
Commitment to resilience means taking accountability from the top all the way down, Sennett says. “It’s the ability to recognize errors quickly and contain them.”
Ultimately, the responsibility for following these principles rests with organizational and safety leadership, the experts say. They must create a culture that allows all workers to speak up and engage in creating a safer work environment that avoids failure.
Understanding Risk Management and Assessment
We have the resources and expert guidance you need to improve how you assess risks to prevent hazards, protect workers and safeguard equipment.
Learn more