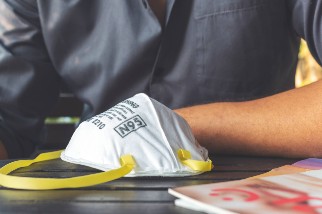
Air contaminants are everywhere — even though we can’t see many of them. We can see about 90% of mists, but only about 10% of dusts.
“You’re breathing in the other 90%,” says Pete Engelbert, CSP, CIH, who has 33 years of experience in safety and industrial hygiene.
This is why it’s so important for safety professionals to acquaint themselves with how to properly select respirators and to know the OSHA rules that govern them.
Engelbert recently conducted a detailed overview on respirators with our Environmental and Industrial Hygiene Practice Specialties. His first piece of advice on using respirators is counterintuitive: Don’t.
“If we talk about any hazard, we can’t forget the hierarchy of controls,” Engelbert says.
“Too many times we pick up a respirator and say, ‘This is the armor for my lungs and I’m OK.’ That’s usually not the case,” he explains.
He recommends eliminating, substituting or reducing the hazards through measures like nontoxic alternative materials, ventilation, enclosures or housekeeping procedures before turning to respirators. But where the situation warrants using respirators, following OSHA procedures and industry best practices will maximize employee safety.
When to Use Respirators
Safety professionals understand the need to protect employees whenever they are exposed to air contaminants. Air contaminants include:
- Dusts: solid particles temporarily suspended in the air
- Mists: liquid particles temporarily suspended
- Fibers and asbestiform minerals: fibers like asbestos or fiberglass
- Fumes: super-heated solid particles (often metal), temporarily suspended in the air because of the heat column
- Gases and vapors: at room temperature, substance that is gas or vapor coming off a liquid
When these air contaminants are present and other measures higher in the hierarchy of controls can’t be achieved, a respiratory protection program is needed.
Using Respirators: 9 Elements Every Program Needs
All employers that require workers to use respirators must establish and maintain a respiratory protection program that complies with OSHA’s 29 CFR 1910.134(c) respiratory protection standard for general industries or 29 CFR 1926.103 for construction. The site-specific respirator program must include the following elements:
- Procedures for selecting respirators
- Medical evaluations of employees using respirators
- Fit testing procedures
- Procedures for proper use
- Procedures and schedules for cleaning, disinfecting, storing, inspecting, repairing, discarding and otherwise maintaining respirators
- Procedures to ensure adequate air quality, quantity and flow of breathing air for atmosphere-supplying respirators
- Employee training on respiratory hazards to which they are exposed
- Employee training on the proper use of respirators, including putting on, removal, limitations and maintenance
- Procedures for regularly evaluating the program’s effectiveness
The program must also have a “suitably trained” administrator. OSHA requires plan administrators to “have competency and special training,” but does not specify what those terms entail. However, AIHA offers details in its 2001 guide, “A Summary of Essential Competencies for Administering a Respirator Program."
Engelbert offers additional tips on several key elements.
Medical Evaluation
While a medical examination is required only once — when an employee begins a respirator program — many companies perform exams annually as a best practice, he adds. “There is no substitute for an employee being seen by a physician or other licensed healthcare professional,” Engelbert says.
The healthcare professional should use the questionnaire provided in OSHA 29 CFR 1910.134(e)(2)(ii) and Sections 1 and 2, part A of Appendix C, and may require additional testing with a spirometer.
Some safety professionals may wonder how the questionnaire interacts with privacy laws such as the Health Insurance Portability and Accountability Act (HIPAA), but Engelbert says the designated program administrator is entitled by OSHA to see the health questionnaire for safety reasons. For example, an employee’s claustrophobia may cause them to tear off a mask or ruptured ear drums may allow a contaminant to enter the body.
Fit Testing
There are two methods for fit testing employees depending on the type of mask. The quantitative method assigns a number, while the qualitative is a go/no go method.
- Tight-fitting half-mask respirators may be fitted with either method
- Tight-fitting full-mask respirators require the quantitative method
- Blast hoods/helmets do not require a fit test because they operate under positive pressure that forces contaminants away from the employee
Evaluating Program Effectiveness
Safety professionals should have the means to prove program effectiveness with data, and the best way is through air monitoring and, where appropriate, biometric testing, Engelbert says.
Selecting and Buying the Right Respirator
Safety professionals can select the right respirator and filter based on the hazard, Engelbert says. To do so, they should follow three steps.
- Step 1: Review the safety data sheet (SDS) under the section listing hazardous components in your materials.
- Step 2: Note the permissible exposure limit (PEL). The PEL is not always included on the SDS, but the threshold limit values or TLVs often are in one of these ways, Engelbert says:
- TLV-TWA: time-weighted average (generally equal to a PEL)
- TLV-STEL (short-term exposure limit): 15-minute exposure with a one-hour rest
- TLV-C: ceiling
While these terms can seem confusing and even conflicting, Engelbert helps define them in the webinar.
Once you select the right respirator and cartridge, you then need to calculate how long the cartridge is effective. For example, organic vapor cartridges have a limited life because vapors deteriorate the charcoal even when sitting on a shelf.
OSHA requires an employer to provide a change-out schedule as part of a respiratory protection program. Some cartridge manufacturers also provide software or phone support to calculate the lifespan of a cartridge, but many employers require workers to change out a cartridge at the end of each shift as a best practice.
“OSHA is historically happy with that,” Engelbert says.
An exception to these rules: A high-efficiency particulate apparatus (HEPA) cartridge can be used until it becomes difficult to breathe through, he adds.
Finally, while these steps can help safety professionals find the right respirator and implement a respiratory protection program, Engelbert emphasizes that this information is intended to familiarize safety professionals with using respirators and is not a substitute for employing a specialized professional or completing training to develop specific skills.
Understanding Risk Management and Assessment
Get the resources and expert guidance you need to improve how you assess risks to prevent hazards, protect workers and safeguard equipment.
Learn more