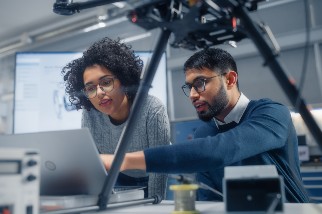
Mitigating risk through design requires your involvement early in the design process — and that means learning to communicate with engineers.
But safety professionals and engineers don’t always speak the same language.
“Safety professionals and engineers are part of the same team; they’re not really competitors, but they see each other as competitors,” says Lawrence Schulze, Ph.D., P.E., CPE, associate professor of industrial engineering at the University of Houston.
Although they share the desire to achieve safe, effective designs, their approaches often differ and communication can break down.
“In every serious incident I’ve investigated, the failure to communicate effectively was always a causal factor in the incident,” says James Junkin, CSP, MSP, SMS, CSHO, CEO of Mariner-Gulf Consulting and Services LLC. “The failure of communication between engineers and safety professionals often occurs because they approach the design and the system with different goals and purposes.”
Engineers’ purpose is to design, build and comprehend a complex system and fundamentally know all aspects of the system, the function of its parts and how they work together, and anticipate what can go wrong and how to fix it. Safety professionals look at the designs with the goal of designing out hazards.
These differences can be overcome with effective communication, Schulze, Junkin and Scott Baranowski, CSP, PMP, EHS manager at an energy utility, say in their recent webinar, “Communicating with Engineers and Safety Professionals,” presented by our Engineering and Training and Communications Practice Specialty Communities.
In fact, improving communication with engineers is vital for safety professionals to successfully do their jobs. Engineers typically control the design process — exactly where safety professionals can most effectively eliminate hazards and mitigate risk.
Additionally, better communication between these two functions can increase productivity, create greater task efficiency, facilitate trust and increase retention, Baranowski says.
The three experts offered strategies and advice for improving communication between safety professionals and engineers.
1. Build Trust Every Day
Engineers are driven by small projects with demonstrable success, Schulze says. Start simple with small projects that allow you to build trust over time through day-to-day interactions.
2. Formulate a Project Charter
Junkin suggests that at the start of a new project, gather input from all stakeholders to create a project charter. This short document describes the entire design project, including scope, objectives, responsibilities and communication pathways. This is a common practice in project management and you can find templates by searching online.
3. Design a Quad Chart to Address a Problem
A quad chart is a table, divided into four boxes, that is used to describe the situation, impact, immediate solution and long-term solution to mitigate the risk. Here’s an example:
Situation | Impact |
Steam is released from a valve located under the stairs in a facility. It creates a slip hazard and promotes algae growth. This requires remediation. | The average cost for a slip and fall injury is $20,000. We have had five slip and fall injuries in this location leading to $100,000 in direct costs. Because these injuries require overtime work, that figure increases to $500,000 with indirect costs. |
Immediate Solution | Long-Term Solution |
Relocate the steam release away from the stairs and operational areas. | Relocate steam release to drain directly as soon as possible and design all future steam release locations this way. |
4. Create a Safe Environment for Collaborative Brainstorming
“Minimizing the contributions of other team members in favor of our own will produce solutions that are not realistic or practical,” Junkin says. So create a space for brainstorming and soliciting engineers’ advice on solutions, asking if/how solutions will affect system function. Also take care to avoid telling them how to do their jobs.
5. Show Respect for Engineers’ Time With Structured Meetings
Junkin recommends scheduling structured meetings, where all documents and day-to-day communications have been reviewed in advance, an agenda is set with clear ownership of items and all participants stick to the timeline.
6. Listen and Take Notes
“An effective safety professional is a good listener,” Junkin says. “Talk with engineers instead of to them, listen to their response, incorporate their ideas, do not present your ideas and concerns as absolute demands, ask questions, stay open-minded and be ready to discuss additional options.”
7. Learn to Speak Their Language and Use Plain Language Instead of Safety Jargon
Safety professionals must become skilled in observing group dynamics, recognizing individual priorities and adapting their communication style when working with engineers and other stakeholders. Understanding what your engineers’ preferred method of communication is — email, in-person, phone — can help too, Baranowski says.
8. Find Ways to Have Respectful Conflicts
“Out of conflict comes innovation,” Junkin says, as long as it remains respectful. The best way to avoid disrespectful conflict is to set the tone early in the project and have open communication throughout.
If you don’t yet have any real communication pathways opened with engineering on your work sites, it’s time to reach out and establish a design team. This may require selling the concept to both engineers and top management, Junkin says. But it’s worth it.
“The most effective way to protect workers is to design out the hazards and eliminate the risks that come with exposure,” he adds.
Understanding Risk Management and Assessment
Get the resources and expert guidance you need to improve how you assess risks to prevent hazards, protect workers and safeguard equipment.
Learn more