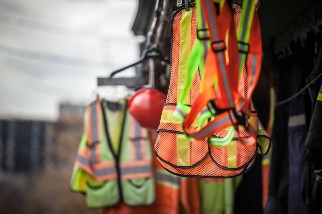
When using the hierarchy of controls, any safety professional would prefer to select solutions from the top by eliminating a hazard completely than the bottom, which requires employees to avoid a hazard through personal protective equipment (PPE).
“However, it seems that some practitioners have turned the hierarchy of controls model on its head,” Gary Morris, Ph.D., CSP, associate professor in the OSH department at Murray State University, and Ryan Cannady, CSP, CIH, STS-C, an ESH manager at UCOR, explain in a recent Professional Safety journal article.
To support their argument, they cite a study, “Risk Assessments: Top 10 Pitfalls and Tips for Improvement,” that found many organizations do not conduct effective risk assessments because they fail to “consider the hierarchy of controls and [fail] to prioritize based on risk.”
While Morris and Cannady identify multiple reasons for this shift, the result is the same: Maintaining the status quo at the cost of employee safety.
The most recent data from the Bureau of Labor Statistics recorded the total number of nonfatal injuries and illnesses in 2022 at more than 2.8 million.
It’s hitting employers’ bottom lines, too. Large-scale research into occupational injury and illness estimates it costs $6 billion for fatal incidents and $186 billion for nonfatal incidents. The study’s author, J. Paul Leigh, describes this amount as “at least as large as the cost of cancer.”
You can move beyond the status quo of prescribing PPE — the “least effective control for protecting employees” — by adopting a more efficient method using the hierarchy of controls.
Why Do We Over Rely on PPE in the Hierarchy of Controls?
To avoid misusing the hierarchy of controls, it’s important to identify why so many companies prioritize PPE over other safety solutions. Companies often choose PPE for the following reasons, despite the drawbacks of each one.
- Many companies look for the cheapest solution to perform the job during the identification and evaluation phases without considering the cost of annual training requirements and PPE maintenance.
- Some companies assume that PPE is also the easiest way to address a hazard with minimal impact on productivity. However, research shows that PPE can “impact human senses and even decrease performance,” Morris and Cannady add. Respirators, for example, can decrease workers’ physical, psychomotor and visual acuity and increase anxiety, a report found.
- When it’s essential to select a solution quickly, many companies turn to PPE first as a stop-gap measure, then fail to consider safety measures higher in the hierarchy as permanent solutions. As a result, “statistics show injuries and fatalities continue to occur in the workplace because the hazards are not being resolved at the source,” Morris and Cannady explain.
- In situations where elimination or substitution methods aren’t immediately clear, companies don’t always consider alternatives.
Taking all these factors into account, it’s clear PPE is not a cure-all for worker safety.
The Methodical Process of the Hierarchy of Controls
Safety professionals should not view the hierarchy of controls as a list of options, but as a hierarchical process to find the best possible solutions.
Morris and Cannady urge safety professionals to move methodically through each element of the hierarchy of controls — from elimination to substitution to engineering controls to administrative controls to PPE — and apply creative solutions.
Additionally, the hierarchy of controls should be introduced at the beginning of any project, not just when things go wrong, says Phill Welch, senior director of EHS&Q digital transformation for EHS software provider ProcessMAP.
“It should be part of the management of change,” he adds. “Too often we see the hierarchy of controls as a trailing indicator when it should be a leading indicator.”
Regardless of which level of the hierarchy of controls you can achieve, you should monitor hazard controls to ensure they were applied correctly and are effective, Welch says.
Step 1: Elimination
Eliminating hazards is the gold standard in the hierarchy of controls. Even in situations where elimination initially seems impossible, safety professionals should explore options.
For example, companies that require employees to work at height may not see any way around the necessity and, therefore, view fall arrest systems as an appropriate safety solution.
But Morris and Cannady suggest that in some cases, the use of drones may be appropriate, such as for residential or industrial inspections.
“Anyone can respond to a fall hazard by implementing fall protection equipment or training, but it is the unique job of a safety professional to investigate ways of removing the employee from the fall hazard,” Morris and Cannady write.
Automated guided vehicles in warehouse operations offer a cutting-edge way to eliminate the dangers of manually operating a forklift while offering companies greater efficiencies, Welch adds.
Step 2: Substitution
The second most effective hazard control is substitution.
One case study Welch described involved the daily use of utility knives to open boxes. Injuries declined significantly after the company switched from traditional utility knives to self-retracting safety utility knives, he says.
Step 3: Engineering Controls
If hazards cannot be designed out from the beginning of the engineering process, a company should consider other engineering and isolation steps to control hazards. Welch suggests isolating equipment in an enclosure, barrier or guard; installing ventilation to redirect chemical hazards; adding a safety light curtain; automating hazardous work where relevant; and implementing ergonomic lifting devices for safer material handling.
Step 4: Administrative Controls
Administrative controls—training, procedures, maintenance, housekeeping and signs—can have a wide impact on employee safety, but they are not often the most effective measure. They are often considered basic safety hygiene that can raise the level of safety awareness overall.
Housekeeping is one of the most low-cost, yet effective administrative controls, Welch says. Keeping a clean, clutter-free workspace can greatly reduce injury and minimize the severity of an incident.
Step 5: PPE
“PPE is the last resort, the last line of defense in protecting an employee from hazards,” Welch says, noting that it creates more work for employees.
If elimination is not possible, then employers should consider PPE in conjunction with other solutions that are higher up in the hierarchy.
“It is critical for those in the safety profession to change the paradigm of choosing PPE first as an easy solution to any workplace hazard,” Morris and Cannady conclude. “Safety professionals must work with production and maintenance to find creative ways of reducing a hazard or eliminating it altogether.”
Understanding Risk Management and Assessment
Get the resources and expert guidance you need to improve how you assess risks to prevent hazards, protect workers and safeguard equipment.
Learn more