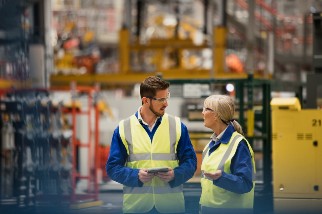
Workplace musculoskeletal disorders (MSDs) affect a company’s financial performance, morale and employee overall well-being.
More than 30% of occupational injuries and illnesses are MSDs. They account for nearly 29% of all workers’ compensation costs and cost U.S. businesses more than $20 billion a year, according to the CDC.
“I cannot recall one work environment where there wasn’t an ergonomic-related risk,” says Bruce Lyon, M.S., CSP, SMS, PE, ARM, CHMM, FASSP, a risk management consultant at insurance broker Brown & Brown. “It’s a big contributing factor for a lot of loss in the U.S. and I think it’s something we should all be interested in.”
An ergonomic risk assessment can provide safety professionals with invaluable insight into the exposures employees face, the severity of those risks and how they might be mitigated.
Our Ergonomics Practice Specialty community invited Lyon and Georgi Popov, Ph.D., CSP, SMS, QEP, ARM, CMC, FASSP, FAIHA, professor in the School of Geoscience, Physics and Safety Sciences at the University of Central Missouri, to review risk assessment tools and a case study during a recent webinar. The experts have written extensively on the topic and developed their own model called the Ergonomic Risk Assessment Tool (ERAT).
Follow the Risk Management Improvement Process
To undertake a complete ergonomic risk assessment, Lyon and Popov recommend using a risk management improvement process with the following steps.
- Establish context and risk criteria. “This is one of the areas we don’t usually do well,” Lyon says of those evaluating ergonomic risk. “If you do a better job on the risk context, you’re going to have a better result.”
- Assess risks.
- Treat risks.
- Monitor and review.
- Record and report.
- Communicate and consult. “This is important and it should be done throughout the whole process,” Lyon says.
Finally, one of the more overlooked factors in managing ergonomic risk is establishing a formal policy that will help safety professionals identify the organization’s overall commitment to reducing ergonomic risk factors.
The formal policy should state the objectives; confirm budgets and resources; establish roles and responsibilities; and ensure ergonomics training.
Methods and Tools for Ergonomic Risk Assessment
Risk assessment is the heart of the risk management improvement model and there are many ways to tackle risk identification, analysis and evaluation. These include common screening tools and checklists such as:
Ergonomic checklists are great for screening and identifying hazards, but while they are easy to use, they can limit identification to just the listed items. Hazards may be missed if they don’t appear on the list, Lyon says.
For full risk assessment, tools like REBA, RULA and ERAT are more appropriate, Lyon says. However, when using these methods it's important to consider what they assess, such as the whole body, upper body or trunk, and the degree of complexity.
The Limitations of Risk Assessment Tools
Popov and Lyon recommend taking several steps to combat these problems and develop a clearer picture of the overall risk.
- One tool is not adequate to conduct a full risk assessment. “Several tools should be used in terms of getting to that complete risk assessment and understanding of the real risk levels and whether they’re acceptable,” Lyon says.
- Many tools only allow an analysis of individual postures. Be sure that the tool you select is the right tool for the motions, positions and body parts you’re evaluating or supplement it with the other tools. Some tools may also not be relevant for employees who engage in unusual positions, Lyon says.
- Consider the synergistic effect of combined ergonomic risk factors. Risk assessment tools account for individual factors such as force, repetition, awkward postures, static postures, contact stress, extreme temperatures, vibration and lighting, contrast and glare. These tools are not designed to measure the amplifying effect that occurs when multiple risk factors combine to produce a higher risk level, Popov says.
- Don’t ignore the importance of training. While employees can be trained on some of the tools quickly, many require specialized ergonomic knowledge or training. Those without it may not complete the assessment correctly or misunderstand the results. The ERAT is one exception. “I’ve trained supervisors within manufacturing in several hours to use the tool to assess their work area and they did a great job,” Lyon says.
Seaweed Removal: An Ergonomic Risk Assessment Case Study
To illustrate these concepts in action, Popov presented a case study during the webinar.
Here’s the scenario: The manager of a beachfront resort was faced with a difficult problem — mountains of stinky seaweed were fouling up the otherwise pristine beach, turning off customers who spent a lot of money to be there.
But removing the slimy seaweed involved shoveling unstable loads of it for 10 to 12 hours at a time in sweltering weather — an ergonomic nightmare that led to a high turnover rate.
The resort conducted an ergonomic risk assessment following these steps:
- Identify the job
- Select the tool
- Identify an assessment team
- Perform the assessment
- Identify corrective measures
- Implement measures
- Verify and refine
By reviewing the OSHA ergonomic assessment checklist, a traditional job hazard analysis, REBA and the NIOSH lifting equation, the resort manager realized the ergonomic risk was unacceptably high and its controls — the implementation of four 15-minute breaks, unlimited water and back belts — were not mitigating the risk.
Management then conducted a bow-tie analysis and used the results to implement changes. They used a frontloader tractor to clear the seaweed, which then still had to be loaded with shoveling. Considering the total risk, management took steps to prevent the seaweed from reaching the beach in the first place through an engineered net.
The ultimate lessons learned: Prevention is preferable to mitigation and no single risk assessment tool can be used to address all ergonomic risk — a truth that is applicable to many ergonomic risk assessments.
Understanding Risk Management and Assessment
Get the resources and expert guidance you need to improve how you assess risks to prevent hazards, protect workers and safeguard equipment.
Learn more