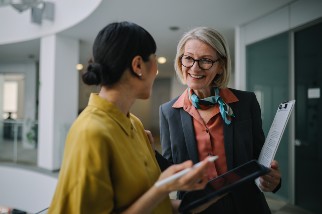
Every safety professional knows how to manage risk, but that doesn’t mean they’re risk management professionals, who conduct coordinated activities that oversee an organization’s overall risk profile.
But by gaining a greater understanding of risk management concepts, you can improve safety and organizational culture, often with greater support from executive leadership.
“The safety profession and the risk management profession have to come together,” says Fran Sehn, M.S., CSP, ARM, principal consultant with FxS Risk and Safety Consulting. “There is a need for them to join forces to improve our whole profession.”
Our Blacks in Safety Excellence (BISE) Common Interest Group and Risk Management Practice Specialty invited Sehn to detail an enhanced risk management model and define the role of occupational safety and health (OSH) professionals in a webinar, “Risk Management for the OSH Professional: Risk Management Differently.”
“We need to have a good foundation from a business standpoint . . . so we can see where we fit and integrate what we do as OSH professionals into that business process,” Sehn says.
A Six-Step Enhanced Model for Risk Management
Risk management involves understanding and anticipating risk and taking steps to reduce or offset that risk. Risk management traditionally follows a straightforward three-step process: 1) identify loss exposures; 2) select techniques to handle the exposures; and 3) implement the techniques.
While this model may meet risk management standards, merely meeting a standard can lead a company to rest on its laurels without truly shifting its organizational culture to seek continuous risk reduction and safety improvement, Sehn says.
Instead, he offers a more comprehensive six-step model for risk management.
Step 1: Establish Risk Management Process With Specific Goals and Objectives
A risk management perspective considers risks to safety, but expands beyond that to encompass property damage and the potential for financial loss. Goals and objectives must address all these aspects.
An example goal for a fictional shopping center would be to reduce injuries to customers and damage to the shopping center to minimize the impact on the company’s operations.
The objectives then might include reducing property losses, lowering the cost of insurance and providing a safe operating environment to decrease injuries.
To achieve these objectives and establish a stronger safety culture, Sehn advocates training staff in risk management principles and methods.
“If we help our entire workforce think in these terms of reducing risk, looking at exposures and making sure they’re part of the team, that’s so much better,” Sehn says.
Step 2: Assess, Identify and Analyze the Risks, Including Sources to Measure and Assess Risk
To assess risk, first detail exposures, which in the shopping center example might include the buildings, parking lots or garages, utilities and related equipment, management and personnel, custodial maintenance, storefronts and food operations, security and environmental concerns.
To identify and analyze risks, consider several categories:
- Human error: Poor training
- Business process: Loss of a key person
- Historical: Events that have occurred such as fire or severe weather
- Geographic: Proximity to hazards, such as a nuclear power plant
- Technological: Power failure, data breach
- Physical: Equipment layout
Assessment tools are also essential in developing a risk score, Sehn says.
Step 3: Develop Business Risk Management Strategies
Many risk management strategies require the expertise of different professionals across multiple departments, but fall along a few paths:
- Risk retention: Accepting the risk posed by a hazard, but relying on a safety professional’s skills to control that risk
- Risk reduction: Implementing tools such as fire protection systems
- Risk transfer: Purchasing insurance
- Risk avoidance: Using subcontractors and employment agencies to move some risk away from the organization
Step 4: Design and Implement Risk Controls
Not every risk reduction intervention will fall to the safety professional to implement, but you will be called on to introduce control methods proven to minimize loss, such as prevention through design, safe driving practices, PPE, lockout/tagout and fall protection, Sehn says.
“We need to have those capabilities and while on the surface they are safety, they are going to help us control and minimize risk,” he says.
Step 5: Monitor Risk Management Performance
While data is important throughout the process, this step is where it becomes critical, Sehn says. Data shows leaders where to focus their attention. Looking at the shopping center example, risk data revealed that while “interior issues” happen more frequently and account for 49% of total incidents, they only cause 17% of incurred losses. Sidewalk-related issues account for 13% of total incidents but make up 49% of total losses.
With sidewalk-related incidents having a greater impact on the organization, safety and organizational leaders can focus on reducing risks through proper maintenance, signage and security cameras that protect against insurance fraud.
Step 6: Implement Continual Improvement
While organizational leaders should constantly look at the data generated by their risk management capabilities to determine improvements, you can take several steps to embrace continual improvement.
- Advance skills and education and share knowledge with other safety professionals.
- Tap resources and training opportunities in risk management. Look to insurance providers because they are incentivized to reduce risk for their clients and often “bring a lot of resources to the table,” Sehn says.
- Develop serious, positive, ongoing relationships with key stakeholders in the business and continue to build these relationships until everyone is on the same page, from workers most vulnerable to risks to executives who focus on bottom-line business practices. Work on those relationships all the time, Sehn says.
- Adopt a strong “process view” of your business. Compared to taking a program view, which has a beginning and end, a process view looks at inputs and outputs continuously.
By understanding risk management beyond safety, you can push the organizational culture to embrace safety and risk reduction with greater buy-in from executives.
Understanding Risk Management and Assessment
Get the resources and expert guidance you need to improve how you assess risks to prevent hazards, protect workers and safeguard equipment.
Learn more