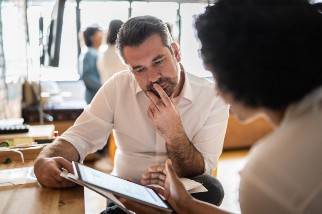
Problem-solving skills are important in any job, but they are the heart of safety, says longtime safety leader and ASSP Fellow Mark Hansen.
“The genesis of safety comes from looking at issues in the workplace and finding out what those problems and hazards are and putting together a mechanism to solve those problems,” he told members of our Engineering Practice Specialty in the webinar, “Problem-Solving Skills — Critical for the Success of Safety Professionals.”
Hansen, P.E., CSP, CPE, CPEA, FASSP, senior ESH manager at Newport News Nuclear BWXT Los Alamos, shared how safety professionals can improve their problem-solving skills and how to get management on board with their solutions.
How to Systematically Solve Problems: Follow the Engineering Design Process
To be more effective at solving problems, Hansen recommends looking to the engineering design process. The same process that leads to new inventions like the lightbulb can help safety professionals think of outside-the-box solutions, he says.
- Define the problem and goal. Identify and briefly describe the issue and the objective, considering the unique requirements, challenges and user.
- Conduct research. Gather information internally about the problem so you can consider it from every angle and identify the limitations and possibilities. Then, investigate existing solutions to similar problems, both within and outside of your industry. Consider technology with similar applications, even if it would require some modification.
- Imagine possible solutions. Hansen always develops multiple solutions to problems, then explores and compares them with a group. He recommends being open-minded during this process, knowing your solution may go through many iterations.
- Choose a solution. This is not an “eeny, meeny, miny, mo” process, Hansen jokes. It’s helpful to have a list of criteria to assess which solution meets which criteria, such as cost, timeline, materials and tools, process changes, hazards, exposures and the environmental or cultural impact. Each solution may meet different criteria. For example, one may meet cost criteria, yet exceeds the timeline. Another may be the safest, but it costs too much. Determine which criteria are most important to help you select the right solution.
- Create and test prototypes. Whenever possible, Hansen prefers to consider multiple prototypes to determine how the solutions operate in their real-world applications. Think not only about the criteria from step four, but also the usability, ease of operation, maintainability and longevity.
- Improve the solution. After implementing the solution, share results and continue to explore how your team could improve the solution, Hansen says. Iterate your solution to make the product the best it can be.
Communication underlines every step of the process and is important both in design and problem-solving; neither can be done successfully without the input of the people who will be directly and indirectly affected by your solution, Hansen says.
The Problem-Solving Process in Action: A Case Study
During the webinar, Scott Baranowski, CSP, PMP, manager in EHS at an energy utility in Charlotte, NC, shared a case study of how he used this process to reduce significant ergonomic hazards to employees using the Gravure printing process.
The Problem: Gravure printing uses cylinders engraved with images to print items like magazines and catalogues. Setting up these cylinders is a highly manual process, Baranowski says. An operator physically lifts, moves and installs both a cylindrical sleeve and bearing assembly into the press machine. These attachments often weigh at least 90 pounds. The process at this facility took place 24 hours a day, through three, eight-hour shifts. Operators might install up to 16 cylinders per shift.
The Process: Baranowski conducted studies, talked with employees and examined various challenges and opportunities. To identify solutions, he explored devices from similar industries and applications and trialed some with operators. His team considered a process change that would have split the load between two operators, but they realized it wouldn’t work. They also explored larger automatic equipment, but space was limited and expansion wasn’t possible because the location was adjacent to a hazardous area.
The Solution: A local vendor devised an optimal solution by modifying a load handling tool to fit the tight area. It allowed both the sleeve and the bearing assembly to sit between two V blocks that were driven together to clamp the objects so they could be installed. This solution allowed operators to perform their job without repeatedly lifting and manually handling the heavy objects.
How to Sell Your Solutions to Management
While selling your ideas to management is not an official step in the engineering design or problem-solving process, safety professionals know it’s essential. Hansen’s unique method is to show management three different solutions he dubs the “Cadillac,” “Chevrolet” or “Volkswagen” solutions. He says you can adopt this kind of method to any three comparable items that resonate with your audience.
The point is to offer different options so they share responsibility in selecting the solution. Management often wants to know two facts above all — how much it will cost and how long it will take — so Hansen packs his presentation with that information. He also presents compelling and convincing research findings whenever possible.
Continually Improve Your Problem-Solving Skills
Once you’re confident in using this process to solve individual problems, you can continuously hone your problem-solving skills in several ways:
- Keep asking why until you find the root cause.
- Brainstorm all solutions.
- Use mind mapping and drawing for visualization.
- Identify opportunities for continued growth and learning.
Safety practitioners are building on an important legacy of problem solving, Hansen says.
“The first safety professionals were insurance inspectors who identified problems in their operations and proposed solutions.”
A Clear Path to Essential Business and Leadership Skills
Not all leaders are the same, or even start out with the goal of becoming leaders. The path to discovering your style and strengths as a safety professional can be challenging without the right resources. We can help.
Learn more